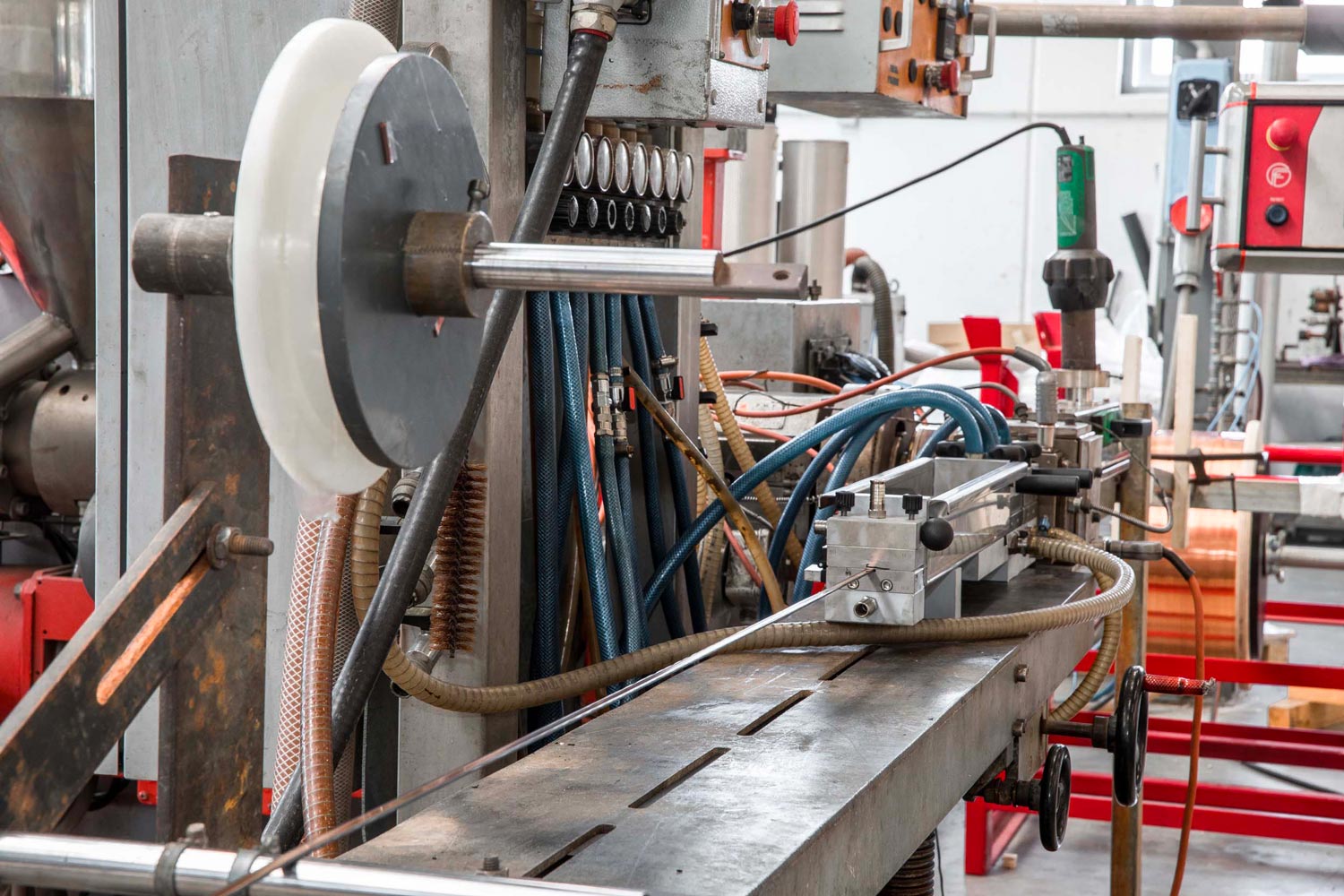
Co-extrusion is an innovative process that allows different materials to be combined together, improving the performance of the finished product. Due to its versatility, this process offers a much wider range of possibilities compared to the solutions granted by extrusion plastics. This technique has evolved considerably in recent decades, becoming a key element in many industries.
What is co-extrusion?
Co-extrusion is a manufacturing technique that involves the simultaneous extrusion of two or more materials that are pushed through a single die, producing an end product that maintains the specific properties of each component. This synergistic combination allows to achieve superior performance compared to using individual plastics for extrusion separately. For example, it is possible to combine the mechanical strength of one polymer with the barrier properties of another, or to combine materials with different aesthetic characteristics. The production process of extrusion and co-extrusion plastics takes place without solvents and is therefore in line with regulations that demand respect for the environment.
The advantages of co-extrusion plastics
Co-extrusion allows a wide range of combinations to be developed. The available solutions are much broader than those offered by extrusion plastics alone. Thermoplastic polymers can be used and combined with fabrics or metals such as aluminum, steel, and copper. It is also possible to adjust the most appropriate plastic composition formula according to the functions the product has to perform or the specific requirements.
One of the main advantages of co-extrusion is the optimization of product performance, as it allows materials with complementary properties such as mechanical strength and flexibility to be combined. From an aesthetic point of view, surfaces with different colors, textures, or finishes can be produced without the need for subsequent treatments that would be required when using extrusion plastics, thus improving the appearance and functionality of the product.
The application fields of co-extrusion plastics
Co-extrusion finds application in many different industries. In construction it is used in the production of window and door profiles, insulating panels, and coatings with weather-resistant layers. In the automotive industry, this technology is used in the manufacture of gaskets, interior components and lightweight yet strong structural parts. The furniture industry uses co-extrusion plastics to make panel and edge coatings with aesthetic finishes and wear resistance. In the electrical industry, co-extrusion is used to create cable jackets with specific insulating properties and technical profiles with special electrical characteristics.
VBN’s ability to co-extrude plastics
VBN has considerable experience in making plastics for extrusion and co-extrusion. VBN can provide expert advice to identify the most suitable production technique for different projects and to manufacture the custom molds for simultaneous processing of different materials. Advanced technological equipment enables co-extrusion processes that make it possible to form profiles with a rigid core and a soft exterior or vice versa soft on the inside and rigid on the surface.
Do you need to make plastics by extrusion or co-extrusion? Contact us and check out VBN’s innovative solutions.