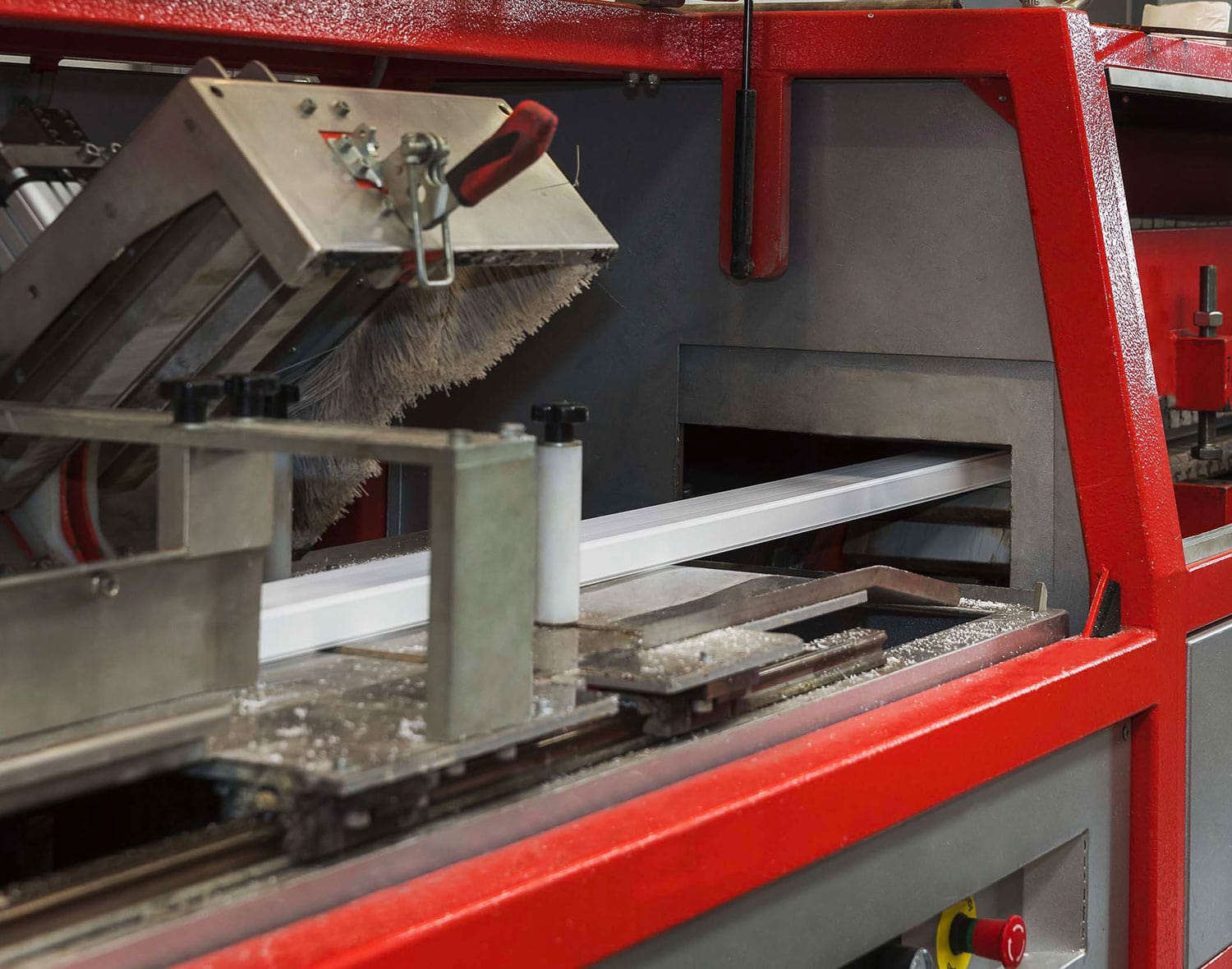
The use of recycled and biodegradable plastics in the production of low-impact profiles is more than just a trend. It represents the evidence of a paradigm shift towards more responsible and efficient manufacturing practices. For decades, the extrusion industry has been dominated by petroleum-derived polymers, which had negative effects on the ecosystem if not properly disposed of. The advent of new raw materials has paved the way for a new era that promises to significantly reduce the ecological footprint. Material revolution is redefining the manufacturing process, allowing to produce profiles with low environmental impact.
Material revolution
Material innovation is the core of this sustainable transformation. The use of recycled plastics and bioplastics as raw materials for the production of environmentally friendly profiles is now a concrete reality. Recycled polymers come from production waste or the reuse of plastic waste otherwise destined for landfill. Reusing these products reduces the need for new petroleum resources and decreases the amount of pollutants that are released into nature.
Bioplastics, on the other hand, are derived from renewable sources such as cornstarch, cellulose or sugarcane. They offer an excellent alternative to traditional fossil fuel-based plastics, allowing to produce profiles with a low environmental impact that are equally good in terms of performance. They can also decompose under natural conditions without leaving any harmful trace in the environment.
Advanced extrusion technologies
In parallel with material evolution, extrusion technologies have also become more and more advanced. Modern environmentally friendly profile production lines are designed to be more energy efficient and optimize the use of raw materials. The processing cycle can reduce energy consumption and minimize the amount of waste that is generated during the manufacturing process. In addition, some of these manufacturing technologies allow the extrusion of polymers with different fusion properties, further expanding the range of environmentally friendly profiles that can be created.
Design for sustainability
Another crucial aspect in the creation of low-impact profiles is sustainability-oriented design. This approach involves the entire product life cycle, from the selection of raw materials to the end of the profile’s useful life. Designers are committed to developing solutions that are not only functional and aesthetically pleasing but also easily recyclable at the end of life. This approach leads to minimize the use of additives that are incompatible with recycling processes and the design of profiles with a low environmental impact that can be easily disassembled and separated into their components to facilitate the recovery of different materials.
VBN’s environmentally friendly profiles
VBN is first and foremost committed to optimizing the processing cycle of environmentally friendly profiles. Through the recovery of production scraps, the use of raw materials can become more efficient, consequently reducing waste. In addition, the extrusion process can be performed with recycled materials, giving new life to post-consumer plastic and turning it into a new resource.
VBN can also process a wide range of polymers, including the latest generation of biodegradable and sustainable plastics.
The energy that powers the company’s departments and produce the environmentally friendly profiles comes from an efficient cogeneration and trigeneration plant.