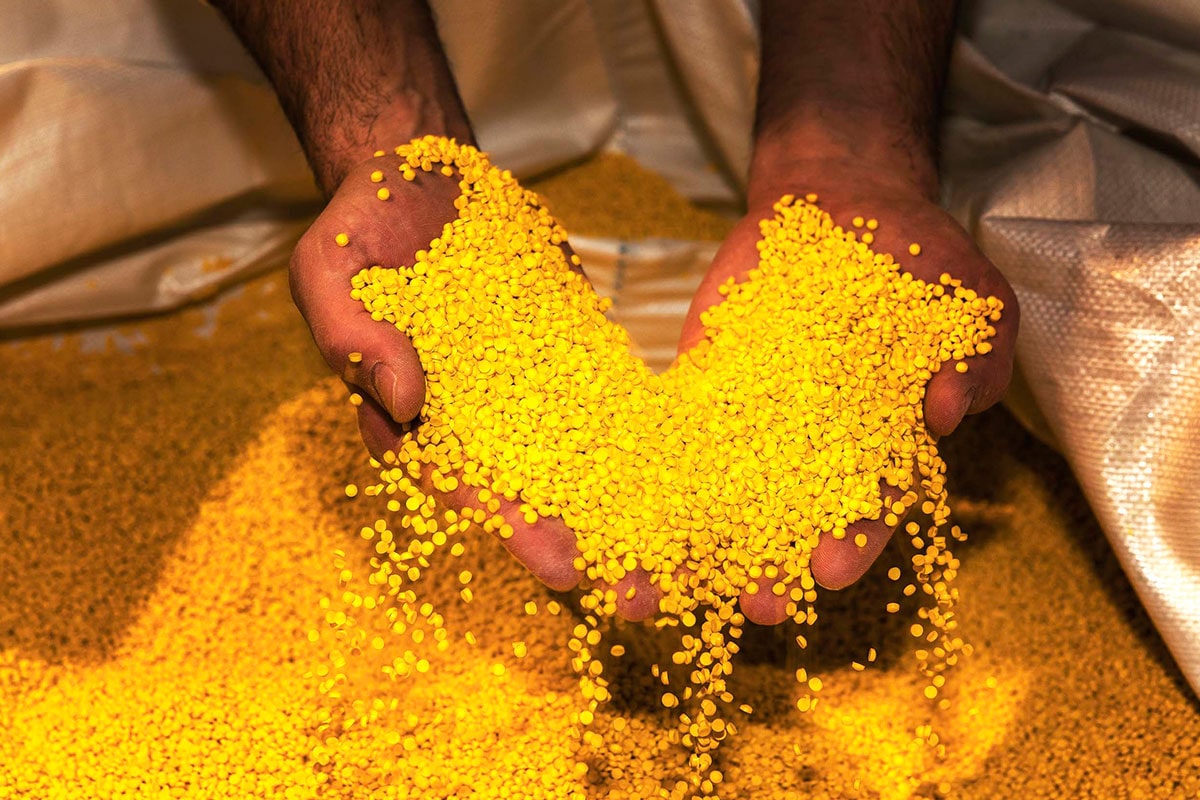
Selecting the right plastic material is crucial to creating a high-quality extruded profile. The choice of a polymer influences the final product performance and durability, as well as the aesthetic result and production costs. We carry a virtually unlimited variety of polymers with different characteristics, and selecting the right compound can be a difficult task. There are a number of factors to consider when choosing the right materials for a project.
Strength and resistance of plastic
When choosing the right plastic material, it is important to consider the loads to which the profile will be subjected and the rate at which they will be applied. If the product must support something heavy, be subject to sudden impacts, or withstand friction, a polymer capable of supporting these forces is required. Similarly, if the profile must be stretched or compressed, a material capable of withstanding this kind of stress is to be used.
If the product must be used underwater or immersed in a liquid, the required type of plastic will need to be waterproof.
Materials that will come into contact with chemicals must be non-corrosive.
Operating temperature of plastic profiles
Even environmental factors, such as temperature, affect the choice of the right plastic material.
Polymers have different melting and heat distortion temperatures. It is important to consider which are the most extreme temperatures to which the product will be subjected, because repeated exposure to heat can cause some plastics to distort their shape and lose their durability. In some cases, such as in applications where safety is important, fire resistance and the ability of a material to generate smoke can be key features during the selection. Moreover, plastic products can become brittle or lose their mechanical properties at low temperatures.
Aesthetic appearance of the plastic profile
During the extrusion process, the choice of plastic material plays a key role not only in ensuring the performance and durability of the final product, but also in determining its aesthetic appearance. Color, finish, clarity and opacity can be key requirements for determining the appeal of a profile. It is important to select polymers that are compatible with the aesthetic result of the extruded item. Specific colors may be required to match the brand’s style or to meet consumer legislation. In addition, plastic extrusion industry is constantly evolving, with new materials and technologies that extend the opportunity to create aesthetically pleasing products. For example, the recycling of plastic materials and the use of biodegradable plastics are gaining ground, responding to consumers’ growing environmental awareness.
Production costs of the profile
The costs of different plastics vary considerably. There are many commercially available polymers that are economically competitive and meet the requirements of most extrusion applications. If special thermal, electrical, or mechanical properties are required, many technical materials can be employed, although they are more expensive. In some cases, very specific plastic materials designed to meet the requirements of a particular application are available. It is important to balance material quality with production costs to ensure the marketing of a competitive profile.
VBN’s advice on the choice of plastic materials.
VBN provides expert advice for choosing the most suitable plastic materials for project implementation. After analyzing the purpose of the profile, its field of use and technical specifications, the most suitable plastic material is identified by evaluating mechanical, chemical, aesthetic, strength and resistance features.
Furthermore, extensive knowledge of raw materials and experience in the processing techniques allow us to find innovative tailor-made compounds to fulfill any requests with highly customized solutions. Upon customers’ request, it is also possible to use raw materials that comply with ROHS, REACH and other international standards.