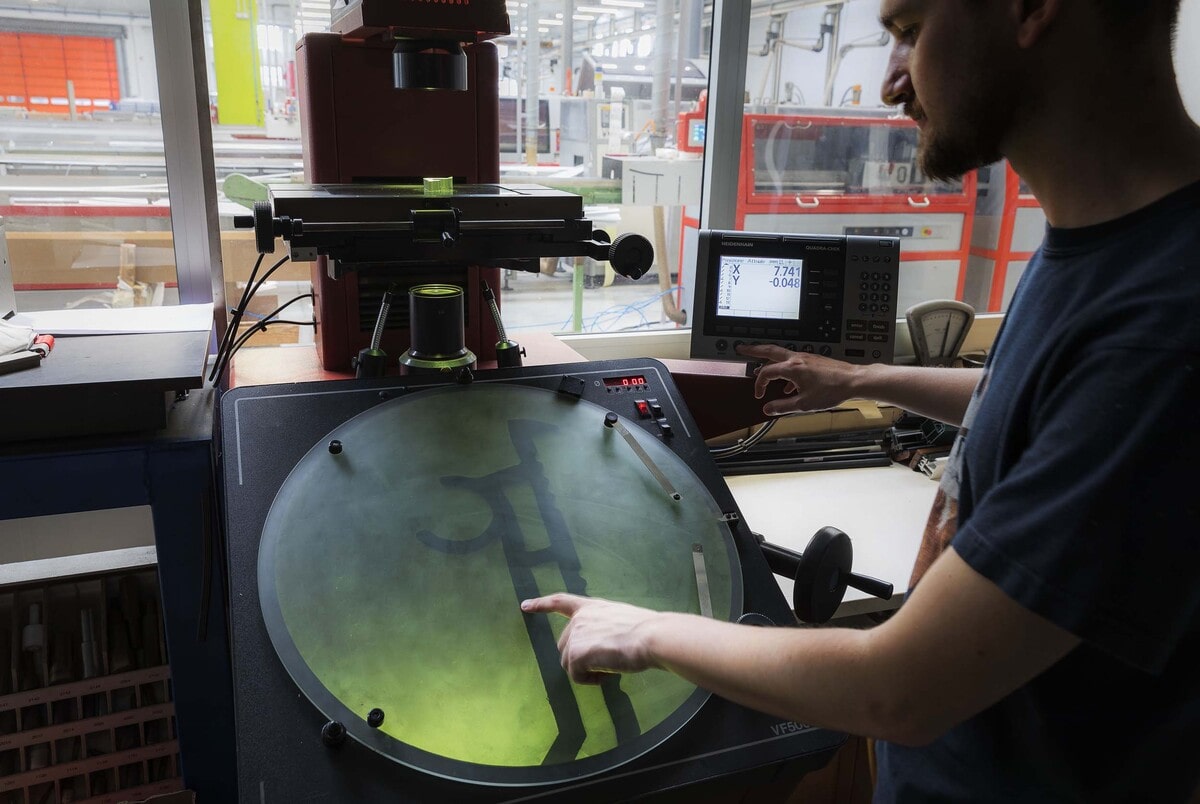
Those who rely on VBN know they can count on an extensive service to produce finished products through plastic extrusion and co-extrusion. The company supports customers with skill and expertise through all the steps necessary to develop quality items made of different types of plastic materials, from the design of the molds to the finishing processes that complete the extrusion operation. With VBN, every project can be realized thanks to the use of 50 different extruders and the possibility to process many different polymers.
The assisted design of plastic profiles
Everything begins with an idea. The customer’s design is the starting point to define the technical specifications related to the application and to carry out a feasibility study. The plastic profile engineering is carried out by the technical department in co-design with the customer. The careful preliminary analysis allows to assess whether the design can be put into production, identifying any critical issues and necessary features. Engineers consider several factors, such as what kind of polymer can be used, profile shape, extrusion temperature, mechanical strength and environmental conditions, material pairings, and many other technical details. Simulation software are often used to test the profile design before actual production.
The consulting on plastic materials
Material choice is essential to realizing any project. After analyzing the function of the profile, its field of application and technical specifications, the most suitable polymer is selected, evaluating its mechanical, chemical, aesthetic, strength and resistance characteristics. The choice of plastic material affects both the physical properties of the finished product and its durability.
Deep knowledge of raw materials and experience in manufacturing techniques enable VBN engineers to find innovative custom compounds to satisfy any request with highly customized solutions.
Prototype production
Once the design and engineering process has been completed, it is time to create a prototype. The model is made using the rapid prototyping technique by starting from the three-dimensional mathematical definition of the object. The prototype is used to test the feasibility of the project and to identify any problems or improvements needed.
It allows the actual aesthetic and mechanical functionality features of the profile to be checked against the project design; and to assess the adequacy of the material and the dimension accuracy in order to provide quick feedback on the production process. Especially when it comes to complex profiles, prototypes allow to verify how different elements fit together and detect any interference. In addition, prototypes allow the customer to see first-hand the future object before putting it into production. Rapid prototyping implies time and cost savings.
Mass production of extruded items
After testing we move on to mass production. Custom molds are created in order to give the desired shape to plastic. During the extrusion process, the extruder pushes the molten polymer into the mold that gives the material a specific shape based on the desired product. VBN has more than 50 extruders with different features that allow the production of an almost infinite range of plastic items. Our assortment of equipment offers a wide range of solutions in profile extrusion by size, screw-barrel combination, hourly productivity, kind of puller and cutter assembly.
Both single-screw and twin-screw extruders are used to produce more complex or particularly large and heavy extrusions.
Mass production of profiles requires strict control of temperature, extrusion speed and other key parameters to ensure the final product’s consistency and quality.
Testing and quality control of plastic profiles
Inspections and tests are part and parcel of VBN’s production philosophy, which is highly quality-oriented. When each production batch is started, the correct setting of the profile extrusion machinery is checked. A preliminary check is carried out to start the equipment and set up the die.
The control stage is repeated several times during production using the latest measurement techniques. In addition, the profile is tested to ensure full compliance with the required specifications during the production process. Quality improvement in production processes and constant updating on extrusion techniques allow VBN to evolve and raise the bar, aiming for excellence.